This is the Larry Neal Butterly Ultralight gyro with the MZ 202 engine and belt drive reduction that Larry flew for a few minutes at Air Venture this summer.
The first thing I did when I got the machine to Mountainair (about 6500 feet and 85 F) was a thrust test. (The hour meter showed 1.35 when I got the gyro to MTA and 1.44 after this test.) I put a 400 pound capacity UPS type package scale with remote readout between the nose wheel and a forklift, zeroed the scale in the horizontal position, loosely tied down the the main wheels and fired up the engine. It was kinda rough running as expected for a 2-stroke running rich at about 2K idle. As I upped the throttle to about 3K, there was a lot of vibration. I let it warm up so the CHT was showing over 200. As I brought the rpm up between 3500 and 4000 the vibration was so strong I thought the prop was coming off and I shut it down. Inspection showed no problem--every thing still tight so I tried again. It sort of smoothed out above 4500 but was not what I would consider comfortable. Still got more severe in the 2500 to 4500 range when I eased it back down.
I found a peak thrust of right at 250 pounds at about 5750 rpm. I got a peak rpm of about 5900 rpm but the thrust was off about 25 pounds at that peak rpm. Leon Massa (the engine and reduction provider) indicated this combination with the right prop can provide around 330 pounds of thrust at sea level. Larry Neal said about 280 pounds at 1300 feet with this prop and had predicted 250 at 6500 feet.
I called up Roger Hooker, the one other BFUL (Butterfly Ultralight Gyro) owner I know of to discuss my experience. He said he had never done a thrust test but had experienced a high level of vibration. He had belt issues in the 3.5 hours he ran his belt reduction unit, including a broken belt and not being able to keep the belt tight. One key thing he mentioned was that the belt would go from tight to loose as he rotated the prop. I then checked mine and sure enough, the belt would go from very tight to more loose with each rotation of the engine.
I got out a dial indicator and figured out how to probe the drive pulley mounted on the engine crankshaft. I found a total swing of nearly 30 thousands of an inch. That resulted in a call to Larry Neal who then consulted with Leon via phone. Larry called me back before I got the pulley off and said to leave it on, strip the engine of anything that could get broken, and send the engine and drive back to Canada (Leon) where he would figure out what the problem was.
After a strenuous effort protectively packing the engine, using lots of rigid foam and tap, I made the 4 hour round trip to Albuquerque to get the 76 pound package to the UPS station. I paid the healthy fee to get it to Canada in a couple days (rather than 2 weeks) which totaled about $500 in materials and shipping fees.
When Leon got it, he found that the drive pulley did indeed have a wobble. He had it pulled off and found 25 to 28 thousands of wobble in the end of the crankshaft. When he had the engine pulled apart, all the components checked out in spec. but the output end support had been moved out of place by the flexing of the output end of the crank shaft. The crankshaft on this engine is multiple pieces that are pressed together with about 20 tons of force. Once everything was pressed back and reassembled the the output wobble was back to just under a thousandth of an inch. Leon also noted that the drive pulley showed a lot of wear, more than he would have expected after 50 or 100 hours of use.
The current thinking is that over-tightening of the belt is what caused the crankshaft output end to get pulled out of place and wobble. The eccentric tension mechanism can exert a great deal of force on the crankshaft if someone uses a cheater bar. Both Roger and Larry have indicated that keeping the belt tight has been an issue and that the belt was either stretching or the eccentric was backing off. The original belt is made of kevlar and the newer one carbon fiber which is supposed to be some 25% stronger. Are either one really supposed to stretch? There is a spec for how much deflection there should be for a given amount of force in the middle of a given amount of unsupported belt length but I don't have these numbers at the moment.
When I get the engine back, I expect to indicate it, run it to see the vibration level, add the belt to spec tension and run and indicate it again. Then add the prop and repeat the above. Then, assuming no wobble or excess vibration has been found, do some extensive ground running to see what if anything happens. I will mark the eccentric to be able to determine if it is backing off or if the belt is stretching.
I just got word the engine is being shipped back from Canada via ground. Expect it will take about 2 weeks to get here.
The engine is back. Leon says the crankshaft has just under a thou of wobble. I measured 7.5 to 8 inside the drive pulley. Leon says they don't hold that to any particular spec. I measured 4.5 to the top of the teeth. Again, they don't hold any particular spec on this but it is machined at the same time as the bottom of the teeth.
I put the belt on and rigged up a way to measure deflection while applying force to the side of the belt. The spec that Leon had for the belt he stocks (mine is actually a different belt but I don't have a spec for it) calls for 3/32 deflection with 21 pounds force in this case. The tangent line is 5.5 inches long as near as I can measure. It is really tricky to get the tension set. You have to get enough force on the clamp so the eccentric will stay put as you tension but not so much you can't tension. I could find no perceptible movement in the eccentric between 12 and 22 pounds of force for the 3/32 deflection using a standard 1/2 inch ratchet to turn the eccentric. This means it would be extremely easy to over tension the belt such that the crankshaft might get pulled off center. The spec really needs to be translated to an eccentric torque spec to make setting easy and accurate.
After several attempts, I ended up with 3/32 deflection at pressures ranging from about 21 to 28 pounds. This means there is still considerable wobble between the drive pulley and the driven pulley.
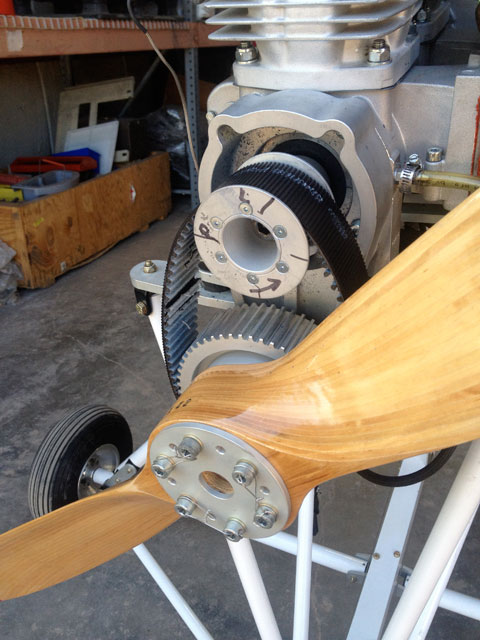
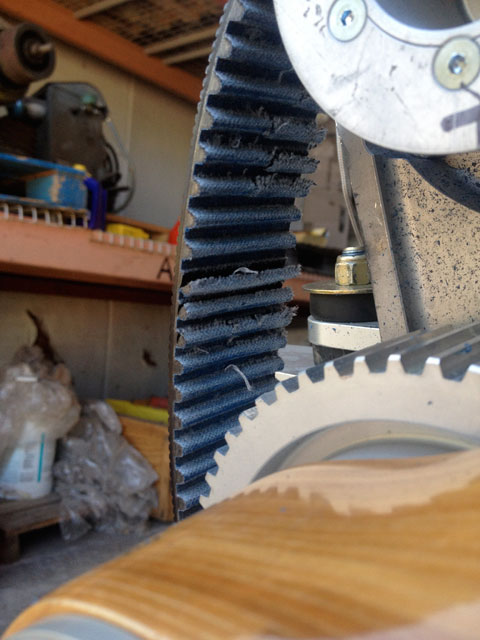
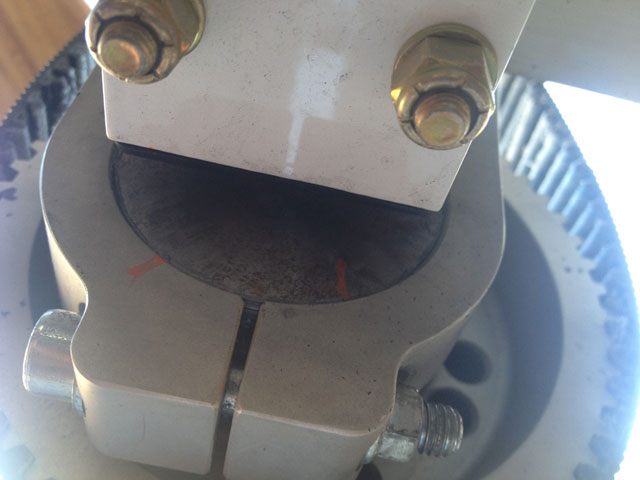
The first thing I did when I got the machine to Mountainair (about 6500 feet and 85 F) was a thrust test. (The hour meter showed 1.35 when I got the gyro to MTA and 1.44 after this test.) I put a 400 pound capacity UPS type package scale with remote readout between the nose wheel and a forklift, zeroed the scale in the horizontal position, loosely tied down the the main wheels and fired up the engine. It was kinda rough running as expected for a 2-stroke running rich at about 2K idle. As I upped the throttle to about 3K, there was a lot of vibration. I let it warm up so the CHT was showing over 200. As I brought the rpm up between 3500 and 4000 the vibration was so strong I thought the prop was coming off and I shut it down. Inspection showed no problem--every thing still tight so I tried again. It sort of smoothed out above 4500 but was not what I would consider comfortable. Still got more severe in the 2500 to 4500 range when I eased it back down.
I found a peak thrust of right at 250 pounds at about 5750 rpm. I got a peak rpm of about 5900 rpm but the thrust was off about 25 pounds at that peak rpm. Leon Massa (the engine and reduction provider) indicated this combination with the right prop can provide around 330 pounds of thrust at sea level. Larry Neal said about 280 pounds at 1300 feet with this prop and had predicted 250 at 6500 feet.
I called up Roger Hooker, the one other BFUL (Butterfly Ultralight Gyro) owner I know of to discuss my experience. He said he had never done a thrust test but had experienced a high level of vibration. He had belt issues in the 3.5 hours he ran his belt reduction unit, including a broken belt and not being able to keep the belt tight. One key thing he mentioned was that the belt would go from tight to loose as he rotated the prop. I then checked mine and sure enough, the belt would go from very tight to more loose with each rotation of the engine.
I got out a dial indicator and figured out how to probe the drive pulley mounted on the engine crankshaft. I found a total swing of nearly 30 thousands of an inch. That resulted in a call to Larry Neal who then consulted with Leon via phone. Larry called me back before I got the pulley off and said to leave it on, strip the engine of anything that could get broken, and send the engine and drive back to Canada (Leon) where he would figure out what the problem was.
After a strenuous effort protectively packing the engine, using lots of rigid foam and tap, I made the 4 hour round trip to Albuquerque to get the 76 pound package to the UPS station. I paid the healthy fee to get it to Canada in a couple days (rather than 2 weeks) which totaled about $500 in materials and shipping fees.
When Leon got it, he found that the drive pulley did indeed have a wobble. He had it pulled off and found 25 to 28 thousands of wobble in the end of the crankshaft. When he had the engine pulled apart, all the components checked out in spec. but the output end support had been moved out of place by the flexing of the output end of the crank shaft. The crankshaft on this engine is multiple pieces that are pressed together with about 20 tons of force. Once everything was pressed back and reassembled the the output wobble was back to just under a thousandth of an inch. Leon also noted that the drive pulley showed a lot of wear, more than he would have expected after 50 or 100 hours of use.
The current thinking is that over-tightening of the belt is what caused the crankshaft output end to get pulled out of place and wobble. The eccentric tension mechanism can exert a great deal of force on the crankshaft if someone uses a cheater bar. Both Roger and Larry have indicated that keeping the belt tight has been an issue and that the belt was either stretching or the eccentric was backing off. The original belt is made of kevlar and the newer one carbon fiber which is supposed to be some 25% stronger. Are either one really supposed to stretch? There is a spec for how much deflection there should be for a given amount of force in the middle of a given amount of unsupported belt length but I don't have these numbers at the moment.
When I get the engine back, I expect to indicate it, run it to see the vibration level, add the belt to spec tension and run and indicate it again. Then add the prop and repeat the above. Then, assuming no wobble or excess vibration has been found, do some extensive ground running to see what if anything happens. I will mark the eccentric to be able to determine if it is backing off or if the belt is stretching.
I just got word the engine is being shipped back from Canada via ground. Expect it will take about 2 weeks to get here.
The engine is back. Leon says the crankshaft has just under a thou of wobble. I measured 7.5 to 8 inside the drive pulley. Leon says they don't hold that to any particular spec. I measured 4.5 to the top of the teeth. Again, they don't hold any particular spec on this but it is machined at the same time as the bottom of the teeth.
I put the belt on and rigged up a way to measure deflection while applying force to the side of the belt. The spec that Leon had for the belt he stocks (mine is actually a different belt but I don't have a spec for it) calls for 3/32 deflection with 21 pounds force in this case. The tangent line is 5.5 inches long as near as I can measure. It is really tricky to get the tension set. You have to get enough force on the clamp so the eccentric will stay put as you tension but not so much you can't tension. I could find no perceptible movement in the eccentric between 12 and 22 pounds of force for the 3/32 deflection using a standard 1/2 inch ratchet to turn the eccentric. This means it would be extremely easy to over tension the belt such that the crankshaft might get pulled off center. The spec really needs to be translated to an eccentric torque spec to make setting easy and accurate.
After several attempts, I ended up with 3/32 deflection at pressures ranging from about 21 to 28 pounds. This means there is still considerable wobble between the drive pulley and the driven pulley.
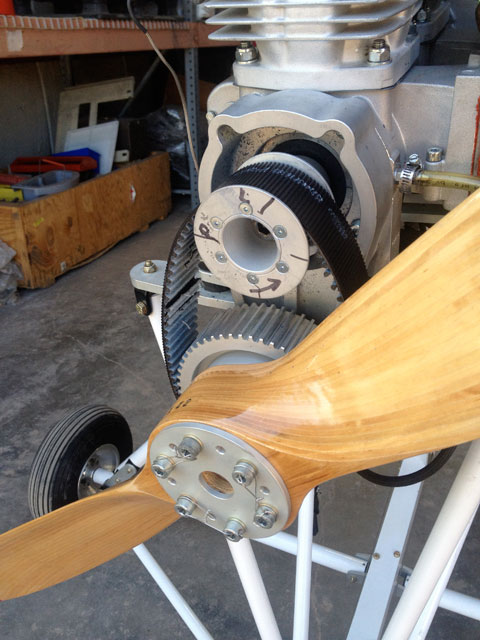
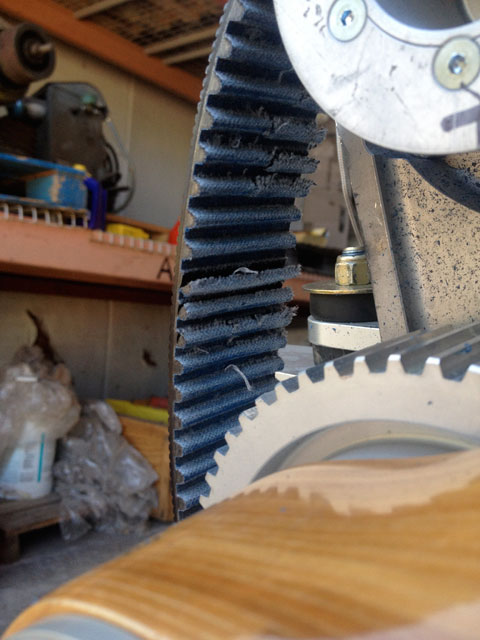
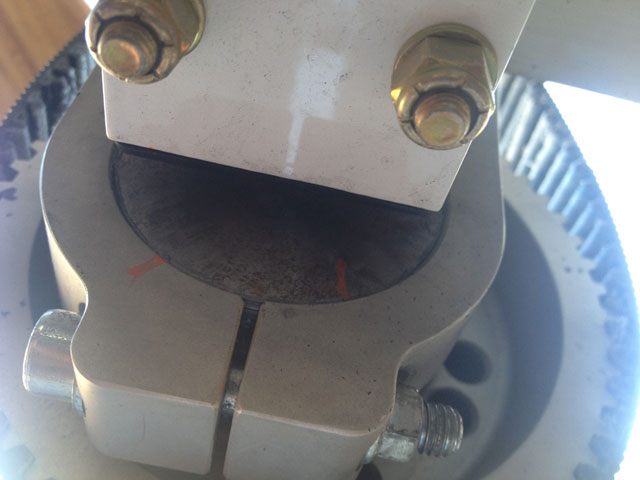
Leave a comment